A lot of studies and methods exist on estimating the overall cost of a project, each ranging in their level of complexity, detail, or prerequisite information that must be available in advance. However, one common principle stands out: the accuracy of a cost estimate solely depends on how much effort is spent on the preliminary design and early engineering phases. One 2018 study by TU Delft published the following:
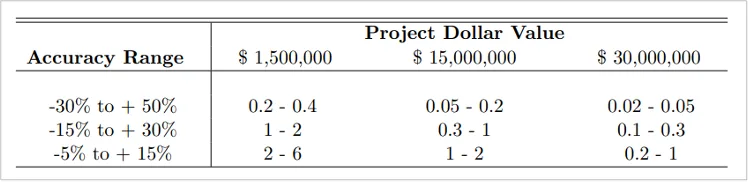
n the figure above (figure 1) the accuracy ranges mentioned can be classified as follows:
- FEL1 (i.e. conceptual design): -30% to +50% accuracy
- FEL 2 (i.e. basic engineering): -15% to +30% accuracy
- FEL3 (or FEED/detailed engineering): -5% to + 15% accuracy
Of course these figures may vary depending on industry and project complexities, but as a general rule of thumb and in average practice, the costs of a detailed engineering study at FEED level for a €1MM project should range from 2-5% of the total project budget. It’s good practice to also add a reasonable contingency to that figure when a project budget is being developed.
The consequences of changes
One other important factor that accompanies inadequate planning is the cost of implementing changes as the project progresses.
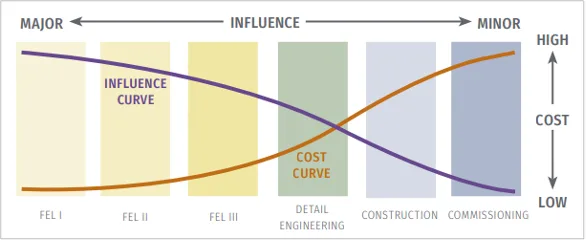
Taking a lot at figure 2 (above), a couple interesting observations can be made:
- The earlier the phases of the planning, the easier and cheaper it is to suggest and implement changes (i.e. the more influence we have on the design and scope).
- As the project progresses that influence is diminished, while the cost of addressing changes increases significantly, because late-stage changes almost always require rework which has an impact on cost and project schedule.
Key takeaways:
- Early investment (in time AND money) is crucial for more accuracy. The quality of your timeline projects, cost estimations, and resource allocations is directly influenced by how much you spend in the early designing, planning, and engineering phases.
- This also has a large impact on how often changes will be encountered during the later phases of the project. Avoiding surprises and the need to change designs lead to significant cost impact.
What causes these budget overruns?
It turns out a lot of work has gone into analysing large-scale projects and their financial performance over the years. What’s interesting is that most of these studies share a lot of common themes regardless of location and time. The two most common factors I could highlight are:
- Lack of key information which leads to improper planning and design, ultimately leading to scope changes.
- Communication issues between project stakeholders (mainly between project owners and contractors).
In one study published by the Civil Engineering Journal in 2019, some interesting figures are given on the cost of design changes across a range of hundreds of projects in Europe, Asia, North America, Africa, and Australia.
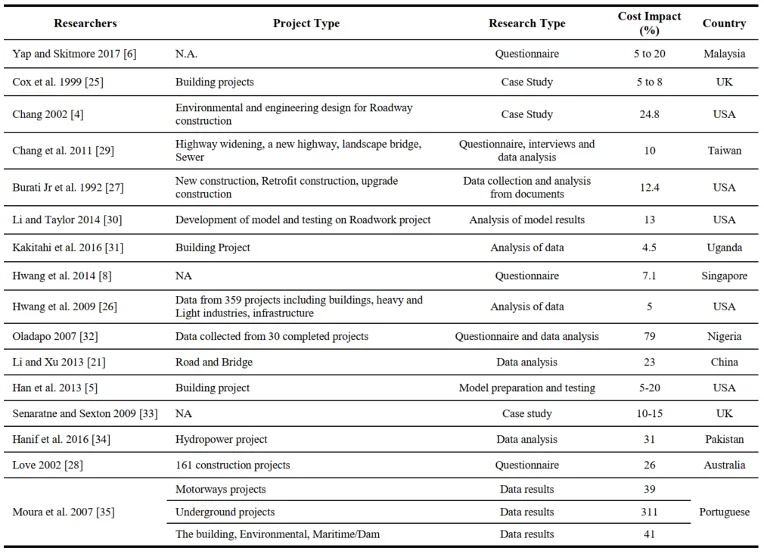
In it, the cost impact of design changes reasonably ranges from 5% all the way up to 40% the cost of the overall project despite some research showing that they can go as high as 79% to 311% in some cases. The causes of these design changes were later broken up into 4 major contributors: clients, designers, contractors, and external factors. However it quickly becomes apparent that the main culprit across all these four parties is improper planning, and inadequate (sometimes lack of) communication during the early design phases.
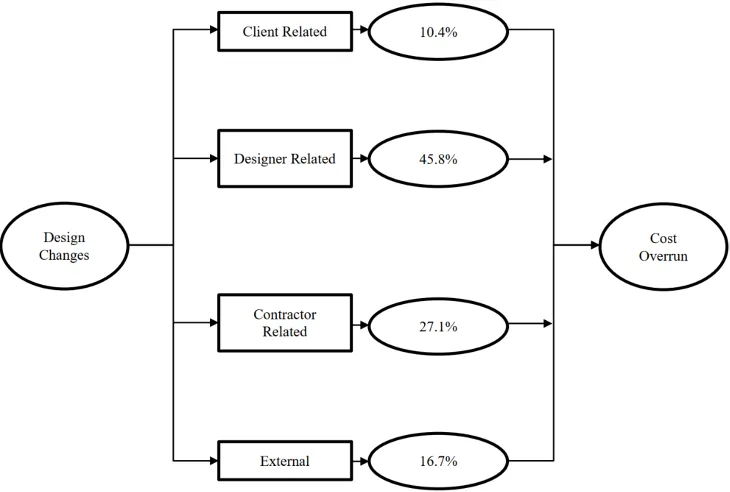
Some examples of how these four factors caused design changes are also mentioned (full list can be found in the study):
- Client (project owner) related causes:
- Lack of technical knowledge (i.e. inadequate planning/preparation)
- Lesser guidance and support available to the clients by the technical persons (i.e. inadequate communication)
- Frequent scope change imposed by the clients (i.e. inadequate planning/preparation)
- Long time taken to make decisions (i.e. inadequate communication)
- Improper financial planning (i.e. inadequate planning/preparation)
- Designer related factors:
- Lack of confidence in preplanning for the design (i.e. inadequate planning/preparation & communication)
- Difficulties in capturing and conveying client needs in conceptual designs (i.e. inadequate communication)
- Poor coordination between clients, designers, and contractors (i.e. inadequate communication)
- No design checks or reviews (i.e. inadequate communication)
- Contractor related factors:
- Inadequate review of design documents (i.e. inadequate communication)
- Awarding contract to the lowest price regardless of quality considerations (i.e. inadequate planning/preparation)
- Lack of communication and coordination (i.e. inadequate communication)
- Poor project organizational structure (i.e. inadequate planning/preparation)
- Incomplete plans and specifications (i.e. inadequate planning/preparation)
- External factors:
- Differing site conditions (i.e. inadequate planning/preparation)
- Unexpected changes in material availability (i.e. inadequate planning/preparation regarding risk management)
- Labor shortages (i.e. inadequate planning/preparation regarding risk management)
- Undetected underground utilities (i.e. inadequate planning/preparation)
In another 2016 study out of Norway for the International Journal of Managing Projects in Business, a sample pool of projects with exceptional increases in cost estimates during the early design phases and concluded that underestimating risks, reliance on weak information without verification, and improper planning at the start inevitably leads to large uncontrolled scope creep and significant costs.
On the other hand, a 2022 student thesis out of University of Twente took a small sample of construction projects in the Netherlands to analyze the causes of cost overruns they experienced. As part of their analysis, they conducted a series of interviews among contractors and clients (project owners) to get their views on what the causes of cost overruns were and how they could be avoided.
They highlight the leading cause of cost overruns is improper cost estimate due to technical factors namely the lack of information during the predesign phase. The next common theme was attributed to improper communication between client and contractor. One interviewee suggested allocating a contingency buffer during cost estimations to cover unforeseen expenses.
Cost overruns are hard to completely avoid. It is important to prepare the project as good as possible to minimize these cost overruns, since scope changes are a big part of cost overruns. However, in order to manage the cost overruns that do appear, it seems that steering on a good collaboration and communication between client and contractor is an important factor to keep costs under control. Other ways to better manage cost overruns as given in the survey and interviews are having a sufficient buffer to absorb cost overruns, having a less risky contract form so that responsibilities are more even between client and contractor, to tender more on quality than on money, so contractors have less incentives to tender for lower prices than realistically possible and also to try and focus even more on the scope when preparing the project.
– Niels van den Top, University of Twente